Glory Tips About What Does MRP Mean
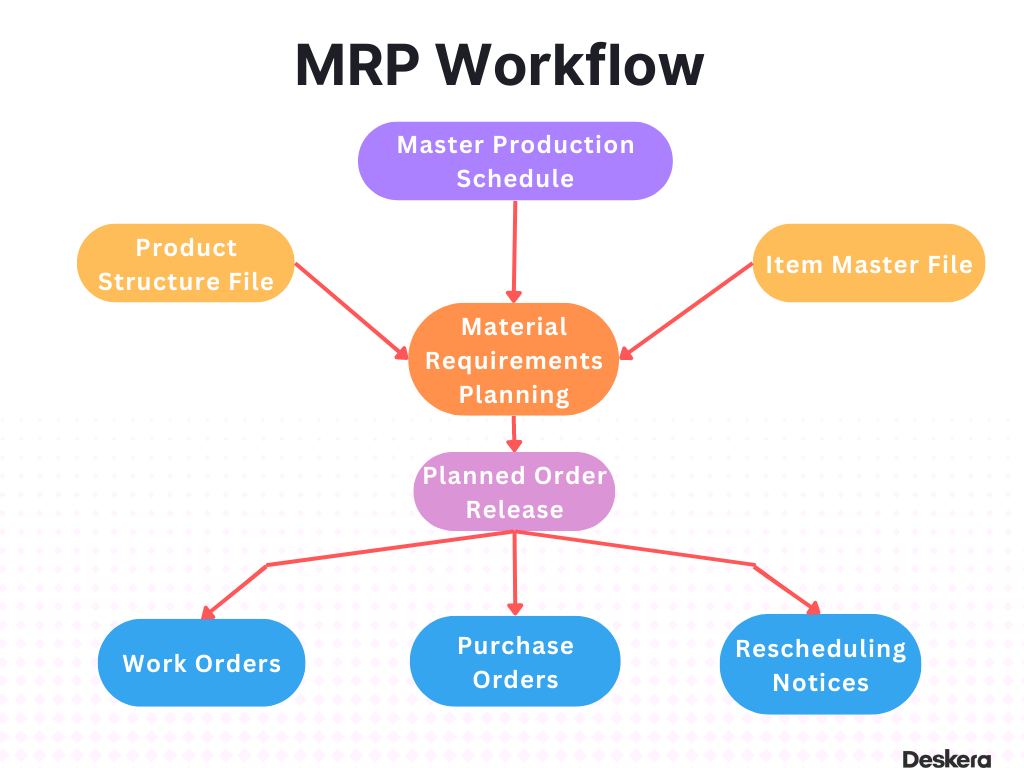
What Is Material Requirements Planning (MRP)?
Decoding MRP
1. What's the Buzz About MRP Anyway?
Ever heard someone casually drop "MRP" in a business meeting and felt a little lost? Don't worry, you're not alone! MRP stands for Material Requirements Planning. It's essentially a computer-based system used to manage and control the flow of materials in a manufacturing process. Think of it as the brain behind keeping production running smoothly — ensuring you have the right stuff, at the right time, in the right place.
But it's more than just some fancy acronym. It's a systematic approach to planning, scheduling, and inventory control. It's about avoiding stockouts that can halt production and preventing excess inventory that ties up valuable capital. It's the Goldilocks of manufacturing, striving for "just right."
Imagine a bakery that needs to bake 100 loaves of bread tomorrow. They can't just start mixing ingredients willy-nilly! They need to know how much flour, yeast, water, and other ingredients they need. MRP helps them figure that out. Without it, they might run out of flour halfway through, leaving customers hungry and the baker stressed.
In essence, MRP provides a roadmap for manufacturers, guiding them through the complex process of converting raw materials into finished goods. It's like having a super-organized checklist for your entire production process, making sure nothing gets missed. And who doesn't love a good checklist?
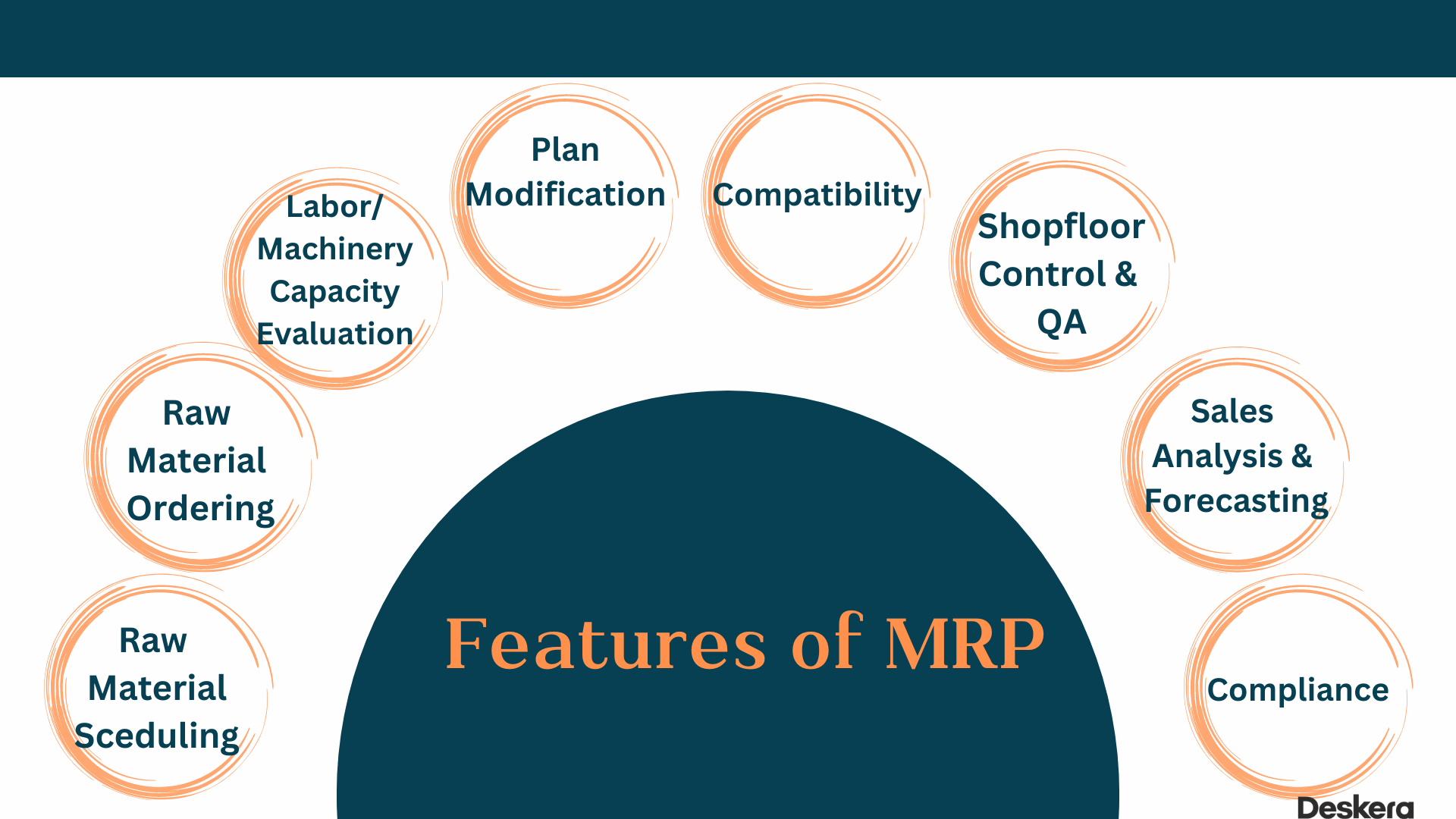
What Is Material Requirements Planning (MRP)?
The Nitty-Gritty of MRP
2. Breaking Down the MRP Process
Okay, so we know MRP is about material planning. But how does it actually do that? It's not magic, though sometimes it feels like it. The process relies on three key pieces of information: a master production schedule, a bill of materials, and inventory records.
The master production schedule (MPS) outlines what needs to be made and when. Think of it as the customer order, or the sales forecast that the manufacturing has promised to deliver. So, If our bakery gets a large order from the local supermarket, that big order would be the key input of the MPS. The next key ingredient is the bill of materials (BOM), that is basically the recipe. It specifies the quantity of each component required to make a single unit of the finished product.
Inventory records provide a snapshot of what's already on hand. This helps to identify potential shortages and avoids unnecessary orders. These three elements are fed into the MRP system, which then crunches the numbers and generates a detailed plan for material procurement and production scheduling. It tells you exactly when to order what, and how much.
Basically, it's like feeding a recipe, a grocery list and a pantry inventory list into a super smart computer and it spits out exactly what you need to buy and when to start cooking so you don't run out of ingredients halfway through Thanksgiving dinner. Okay, maybe not exactly like that. But close!
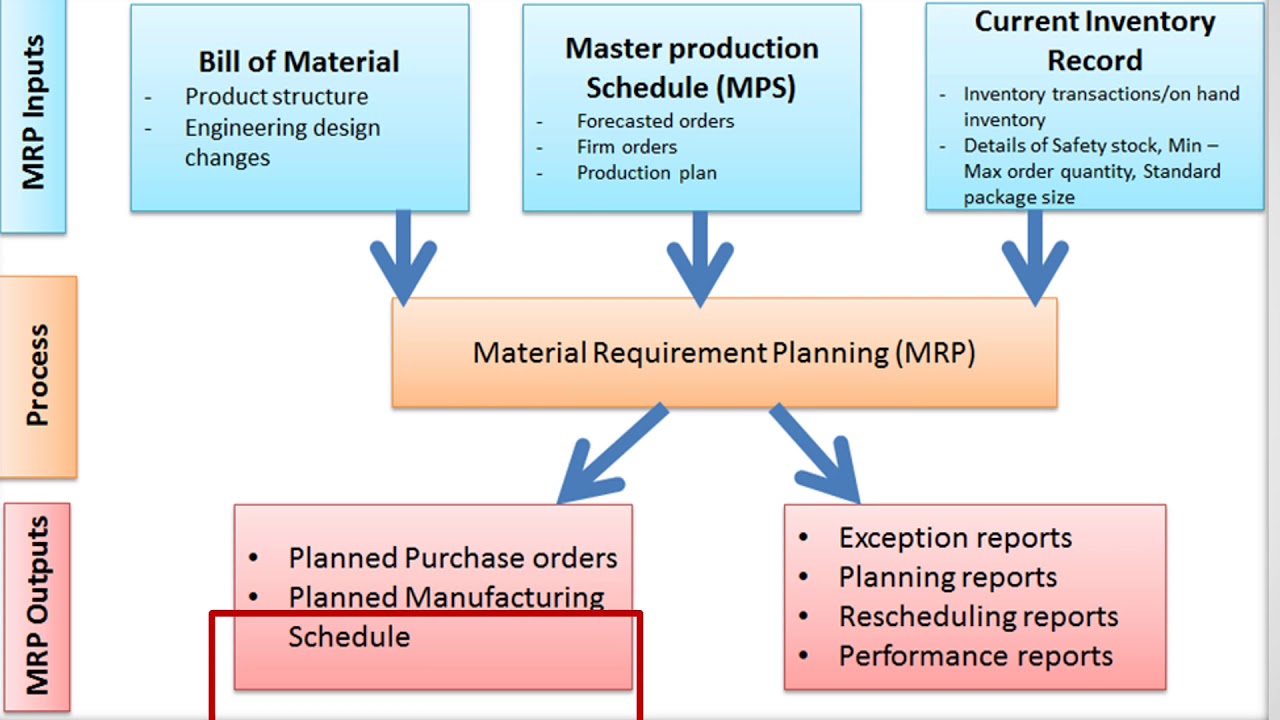
Beyond the Basics
3. Why Bother With MRP in the First Place?
Implementing an MRP system might seem like a daunting task, but the benefits can be substantial. Improved inventory control is a big one. By accurately forecasting material needs, companies can reduce both stockouts and excess inventory, freeing up capital and warehouse space. This is a huge relief for any business trying to manage costs.
Better production planning and scheduling are another key advantage. With a clear understanding of material availability, companies can create more realistic production schedules, reducing lead times and improving on-time delivery performance. Think of how much happier your customers will be when they get their orders on time!
MRP can also lead to reduced material costs. By optimizing purchasing decisions and negotiating better deals with suppliers, companies can significantly lower their material expenses. Every penny saved is a penny earned, after all. That's money you can reinvest in your business or use to buy that fancy coffee machine you've been eyeing.
Overall, MRP helps companies streamline their operations, improve efficiency, and boost profitability. It's not a magic bullet, but it can be a powerful tool in the right hands. The result is a more responsive, more cost-effective, and more competitive manufacturing business. And who doesn't want that?
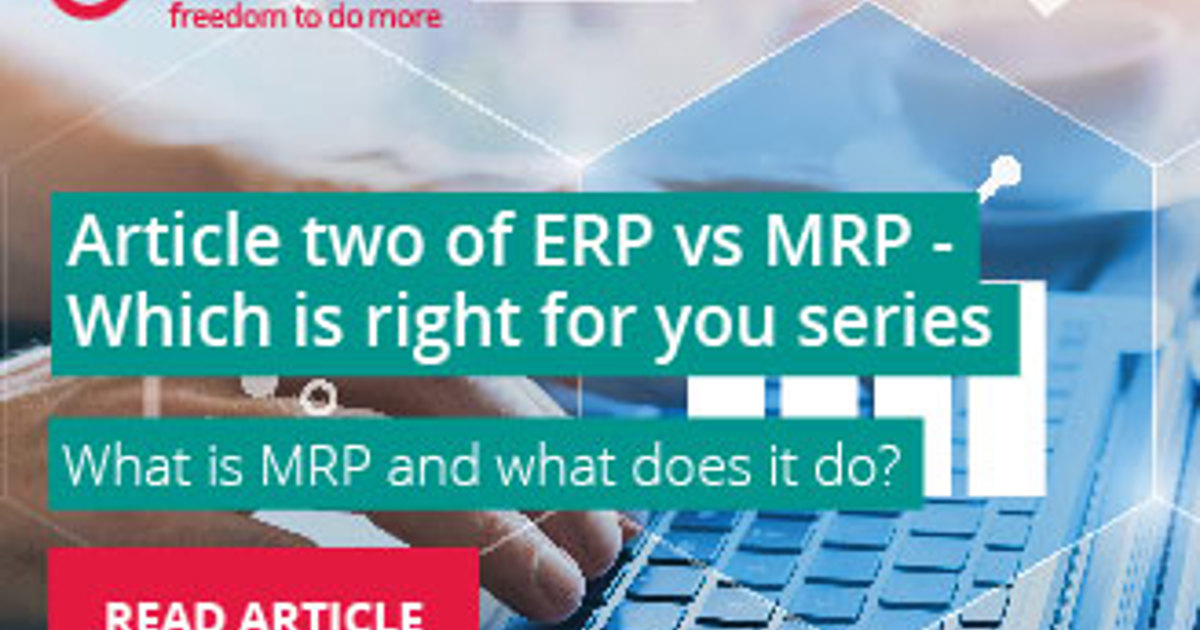
MRP vs. ERP
4. Is MRP the Same as ERP?
You might be thinking, "Wait a minute, isn't this ERP thing also about planning resources?" And you'd be right! Enterprise Resource Planning (ERP) systems are a broader category of software that encompass MRP. Think of MRP as a specialized subset within the larger ERP landscape. ERP systems integrate various business functions, such as finance, human resources, and customer relationship management (CRM), in addition to material planning.
MRP focuses specifically on managing materials and production. ERP, on the other hand, provides a holistic view of the entire organization. So, while MRP helps you ensure you have enough flour for your bread, ERP helps you manage everything from employee payroll to customer orders and marketing campaigns.
In short, MRP is like a specialized tool in a larger toolbox. An ERP system has many tool inside it but MRP is an individual. If you are a small manufacturer, MRP might be sufficient to meet your needs. However, as your business grows and becomes more complex, an ERP system may be a better fit. It's about choosing the right tool for the job.
The key takeaway is that MRP is a focused solution for material planning, while ERP is a comprehensive solution for managing all aspects of a business. Understanding the difference can help you make the right software investment for your organization. It's like choosing between a screwdriver and a full set of power tools. It all depends on what you're trying to build.

Modern MRP
5. The Future of Material Requirements Planning
MRP isn't stuck in the past. Modern MRP systems are embracing new technologies like cloud computing, artificial intelligence (AI), and the Internet of Things (IoT) to become even more powerful and user-friendly. Cloud-based MRP systems offer greater flexibility, scalability, and accessibility compared to traditional on-premise solutions. You can access your data from anywhere, at any time, as long as you have an internet connection.
AI is being used to improve demand forecasting, optimize production schedules, and automate various MRP tasks. Imagine an MRP system that can automatically adjust production plans based on real-time data and predict potential bottlenecks before they even occur. That's the power of AI-driven MRP. The integration of IoT sensors can provide real-time visibility into material levels and equipment performance, enabling proactive maintenance and preventing costly downtime.
This means that you no longer have to be in a brick and mortar building anymore. You can manage the process remotely. This will save money and allow for more productivity overall. It is even more powerful to implement these newer tools than older systems.
As technology continues to evolve, MRP will undoubtedly become even more sophisticated and integrated with other business systems. The future of MRP is about creating a more intelligent, responsive, and agile supply chain that can adapt to the ever-changing demands of the market. So, buckle up and get ready for the ride!

FAQ
6. Your Burning MRP Questions Answered
Still have some questions about MRP? No problem! Here are some frequently asked questions to help clear things up.
7. Q
A: MRP is primarily designed for manufacturing companies that produce physical goods. However, variations can be adapted for service-based businesses with specific resource planning needs.
8. Q
A: The cost of MRP implementation can vary widely depending on the size and complexity of the business, the chosen software solution, and the level of customization required. Cloud-based solutions often have lower upfront costs compared to on-premise systems.
9. Q
A: Implementation time can range from a few weeks to several months, depending on the scope of the project and the resources available. Proper planning and training are essential for a successful implementation.