Casual Tips About What Is A 150% BOM
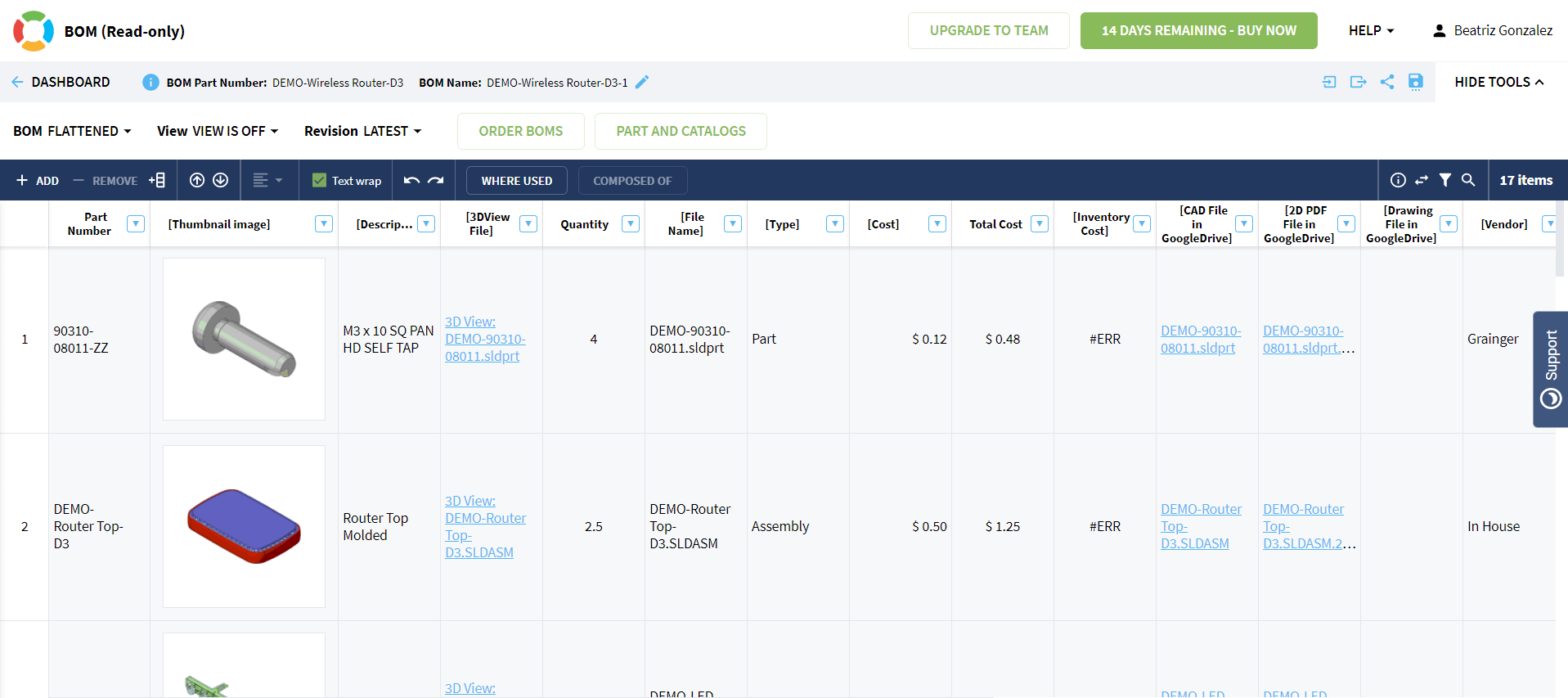
BOM Types OpenBOM Training Library
Unlocking the Mystery of the 150% BOM
1. What Exactly Is This 150% BOM Thing?
Okay, so you've stumbled across the term "150% BOM," and you're probably thinking, "Wait, am I paying extra for something? Is this some kind of inventory conspiracy?" Relax! It's not usually about spending more money. A 150% Bill of Materials (BOM) is essentially a strategic planning tool. It's all about anticipating the unexpected in your manufacturing process — like that time you swore you had enough screws and then realized you were three short on the last unit.
Think of it as a safety net. A standard BOM lists all the components needed to create a single finished product. The 150% BOM? It factors in potential losses during production. We're talking about scrap, spoilage, testing mishaps, and those "oops" moments that, let's be honest, happen to the best of us. It's like adding a little extra sugar to your baking recipe, just in case some magically disappears before it gets into the oven.
So, where does that 150% come from? It's not a magical number pulled from thin air. It represents the anticipated material needs beyond what's theoretically required. The percentage applied to the BOM is based on historical data, industry standards, the complexity of the product, and the skill level of your manufacturing team. For a really complex product with a higher chance of errors, you might even see a BOM over 100% - as high as 200% or even higher. This is to ensure enough materials in hand for unexpected occurrences, preventing delays.
Basically, a 150% BOM means you're budgeting for 50% more materials than theoretically needed. It doesn't always mean you will use that extra 50%, but it's there if you need it. This helps avoid last-minute scrambles for parts and keeps your production line humming along nicely. It's all about preparedness, baby!
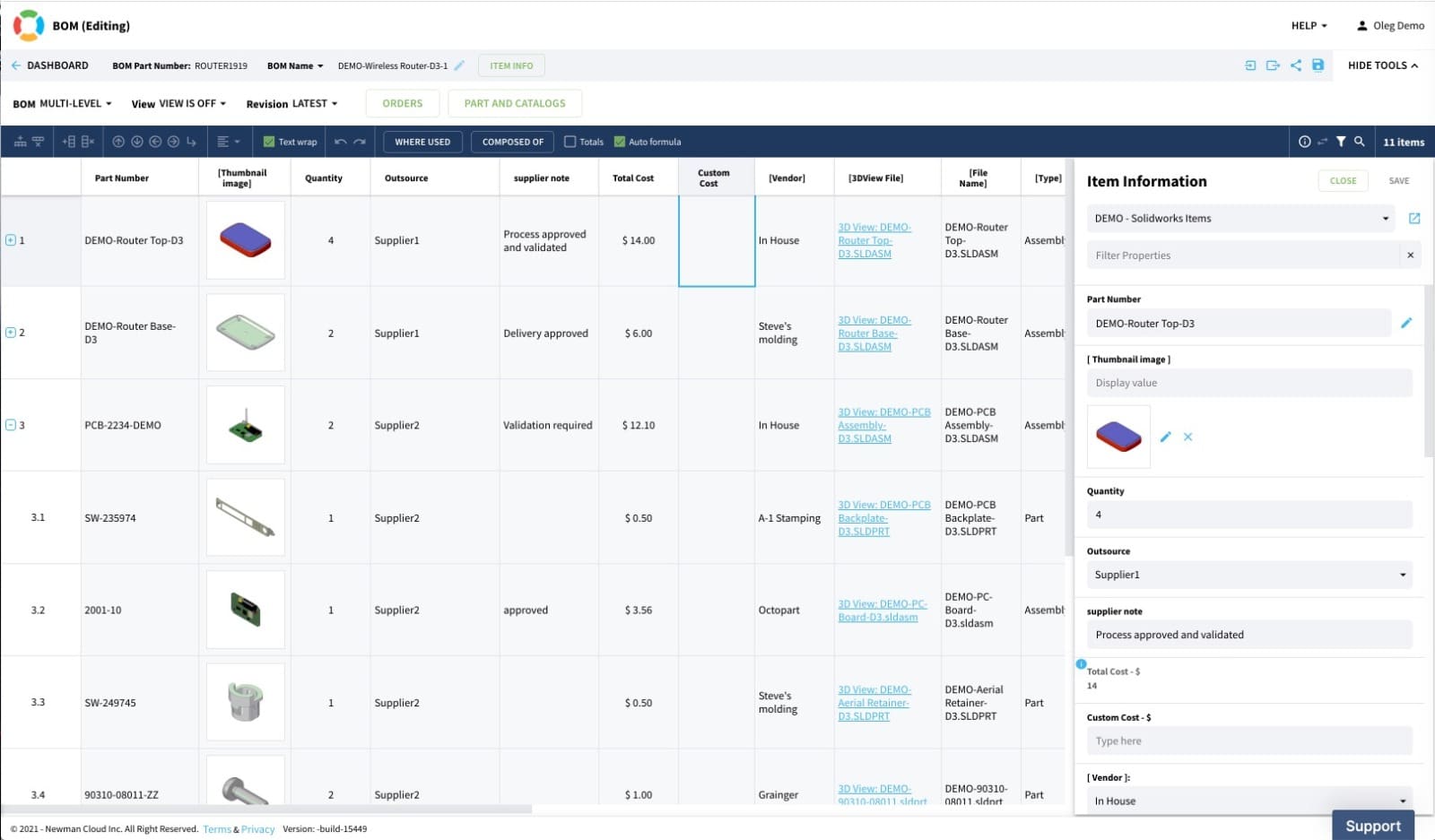
Bill Of Materials Bom Definition Vrogue.co
Why Bother With a 150% BOM? Isn't That Wasteful?
2. The Surprisingly Smart Reasons Behind Over-Provisioning
Now, I know what you're thinking: "Isn't all that extra material just going to end up collecting dust in the warehouse, or worse, in the landfill?" And that's a fair question! But hear me out. The benefits of a 150% BOM, or a BOM adjusted for expected loss, can outweigh the perceived wastefulness, especially if you're smart about how you manage it.
First off, think about downtime. If your production line grinds to a halt because you're short on a crucial component, the cost of that downtime can be significantly higher than the cost of the extra materials. We're talking lost revenue, delayed shipments, and potentially unhappy customers. A 150% BOM helps prevent those costly interruptions.
Then there's the issue of lead times. In today's global supply chain, getting your hands on specific parts can take weeks, or even months. If you suddenly discover you're short on something, you could be stuck waiting ages for a new shipment to arrive. Having a buffer stock allows you to keep producing while you wait, minimizing disruption.
Finally, consider the cost of rework. If you're forced to use substandard materials because you're running low, you might end up with a product that doesn't meet your quality standards. This can lead to costly rework, returns, and damage to your reputation. A 150% BOM allows you to be more selective about the materials you use, ensuring higher quality and fewer headaches down the line. Plus, any leftover, unused materials can often be used in future production runs or potentially even sold off, recouping some of the initial investment. It's a win-win...mostly.
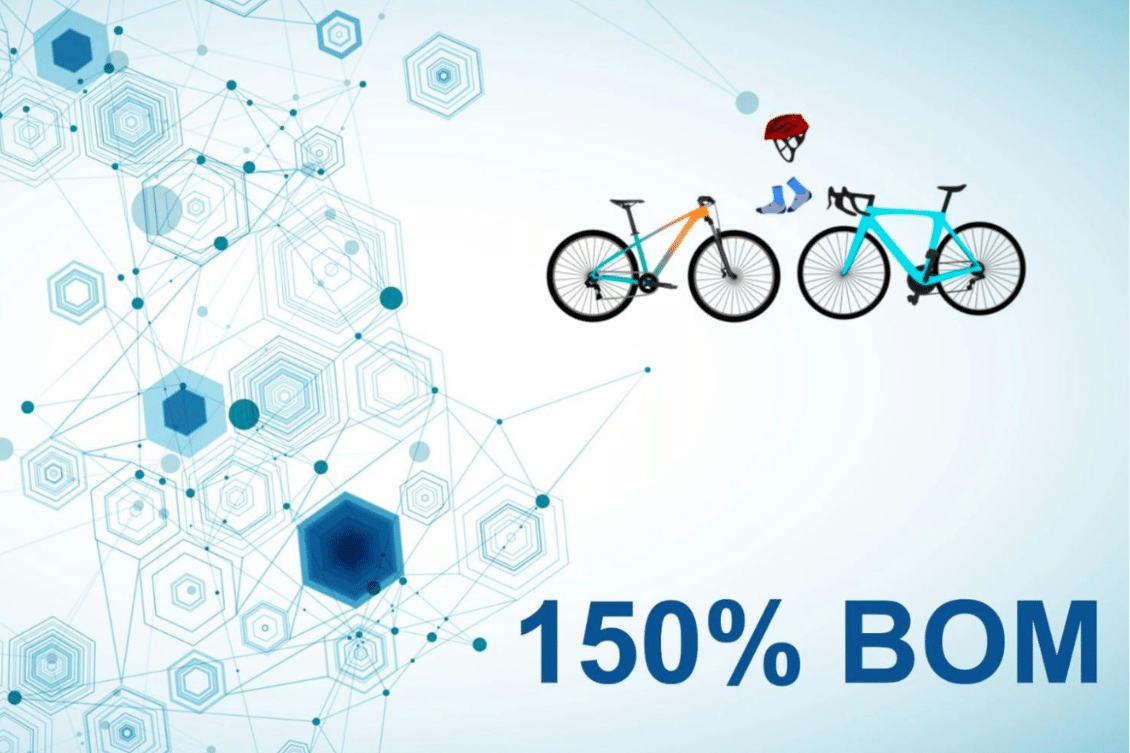
How to Calculate (and Use) a 150% BOM Like a Pro
3. From Spreadsheets to Sanity
Okay, so you're sold on the idea of a 150% BOM (or at least intrigued). Now, how do you actually do it? Fortunately, it's not rocket science, although understanding the underlying data will certainly help the process.
Start with your standard BOM. This is your baseline, the list of exactly what you need to build one unit of your product. Now, look at your historical data. What's your average scrap rate? How often do parts get damaged during assembly? Talk to your production team. Where do they typically encounter problems? All this information will help you determine the appropriate "loss factor" to apply to your BOM.
For example, let's say your standard BOM calls for 10 screws per unit. If you've historically lost 5% of your screws during production, you'd add 5% to your BOM, bringing the total to 10.5 screws. For a 150% BOM calculation, you will multiply your original part count, in this case the 10 screws by 1.5 to arrive at 15 screws in total.
Important! Its worth nothing that the 150% BOM calculation is not always linear. Sometimes a 150% BOM is applied to critical elements that could bring production to a standstill in the event of damage or loss. In other cases it may be necessary to apply the safety margin at different percentages to different components and raw materials. Work closely with your supply chain and operations departments to calculate the right levels to mitigate most business risks for your particular operations.

Beyond 150%
4. Adjusting for Reality
While a 150% BOM can be a great starting point, it's not a one-size-fits-all solution. The ideal percentage will vary depending on several factors, and you'll need to fine-tune your approach over time to optimize efficiency and minimize waste.
Consider the complexity of your product. If you're building something relatively simple with a low risk of errors, a lower percentage might be sufficient. Conversely, if you're dealing with a highly complex product that requires specialized skills and equipment, you might need a higher percentage to account for potential mishaps.
Also, think about the cost of the components themselves. For inexpensive, readily available parts, it might make sense to err on the side of caution and maintain a larger buffer stock. But for expensive, hard-to-find components, you'll want to be more precise in your calculations to avoid tying up too much capital.
The skills of your manufacturing team also play a huge part. A highly skilled and experienced team is less likely to make mistakes, so you can probably get away with a lower percentage. But if you're working with a newer or less experienced team, it's wise to add a bit more padding to your BOM.
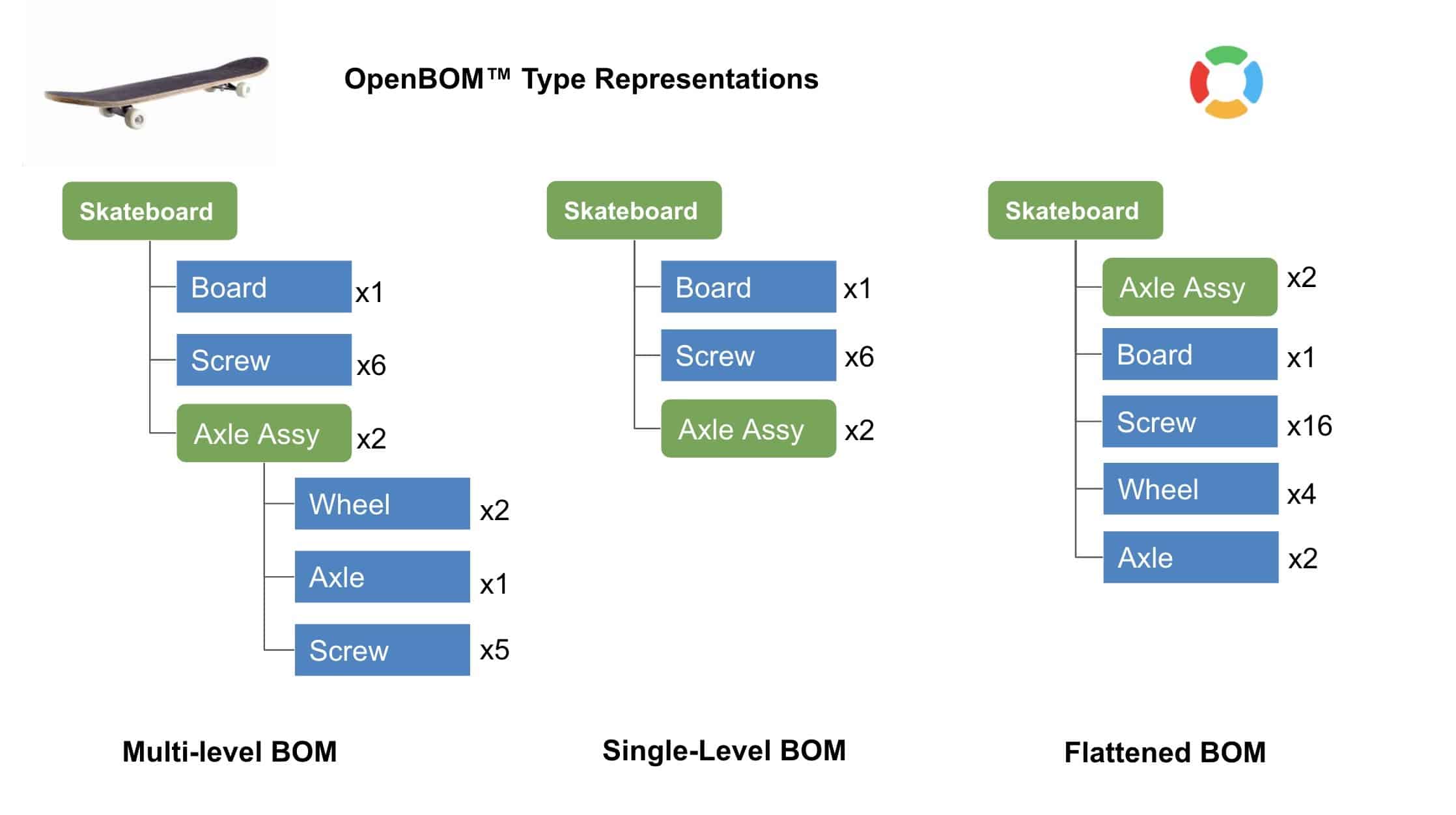
OpenBOM 101 BOM Types MultiLevel, SingleLevel, Flattened
Real-World Example of 150% BOM in Electronics Manufacturing
5. A Case Study
Let's imagine a company that produces circuit boards. The standard BOM for one of their boards lists 100 resistors. However, through experience, they've learned that about 5% of the resistors are damaged during the soldering process. Furthermore, another 2% are found to be defective upon testing the assembled boards. The circuit board manufacturer then applies a further safety factor by applying a 150% BOM calculation.
Without a 150% BOM, the company would frequently run out of resistors, leading to production delays and increased costs. The 150% BOM ensures they have enough resistors on hand to cover any potential losses, and prevent delays. This has a direct impact on their ability to meet deadlines and maintain customer satisfaction.
Moreover, they utilize leftover resistors from the 150% BOM in subsequent production runs, reducing the overall material costs and waste. It allows them to adjust their BOM strategy based on actual production results and supply chain dynamics. The manufacturer would have the ability to be more flexible. This is especially useful when working with external clients to manage the risks of their own supply chains. The client may not necessarily use the 150% but in some cases will require that the manufacturer holds materials equivalent to the calculation.
By adopting a 150% BOM strategy, the company mitigates the risks associated with material shortages, and allows them to focus on innovation, and expanding their business without being hampered by operational inefficiencies. Using historical data and fine tuning their BOM strategy, the electronics manufacturer significantly reduces the impact of supply chain disruptions on their business operations.
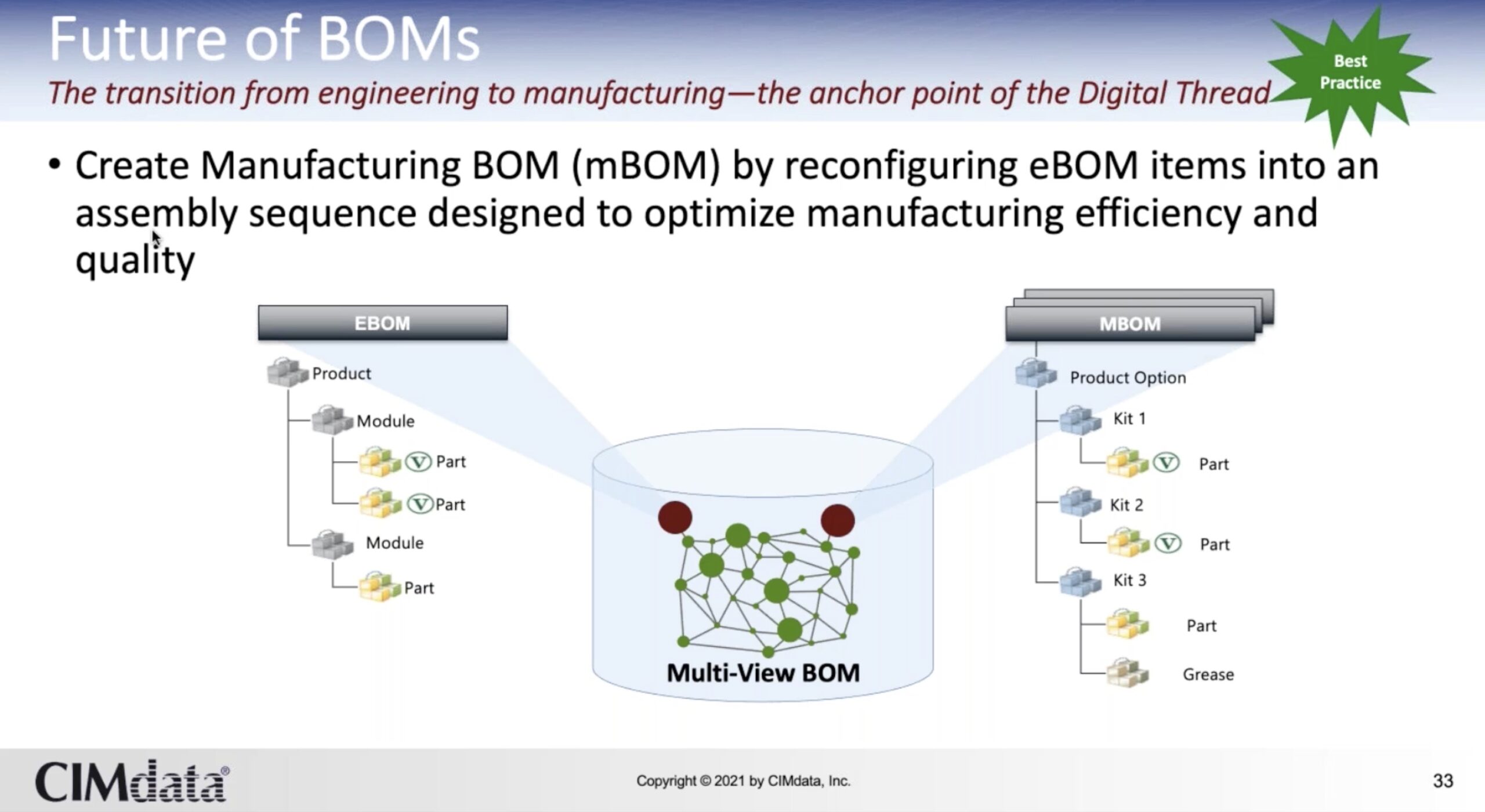
FAQ
6. Your Burning Questions Answered (Hopefully with a Smile)
Still scratching your head? Here are a few common questions about 150% BOMs:
Q: Does a 150% BOM mean I'm always going to have 50% extra material lying around?A: Not necessarily! It's a target, not a guarantee. You might use all the extra material, or you might not. The goal is to have it available if you need it. And if you consistently have a lot of material left over, it might be time to re-evaluate your loss factor.
Q: Is a 150% BOM always the right number?A: Nope! It's just a starting point. The ideal percentage depends on your specific circumstances. Analyze your data, talk to your team, and adjust as needed.
Q: Can I use a 150% BOM for everything?A: You could, but it might not be the most efficient approach. Consider the cost and availability of each component. For inexpensive, readily available parts, a higher percentage might be fine. But for expensive, hard-to-find components, you'll want to be more precise.